お知らせ
檜の引き出しのこと
引き出しから、ふと檜の香り
〝引き出しを開けると、檜(ヒノキ)の香りがする〟- とても些細なことかもしれませんが、杉工場が大切にしていることの一つです。日本の檜は、建材として最高品質とされており、耐久性や保存性にも優れている木材です。杉工場の引き出しの多くは、この国産のヒノキ材を採用しています。材料、構造、材質、香り、細部に至るまでこだわり「檜の引き出し」づくりに取り組んでいます。
無塗装仕上げで、自然のままの香りを
日本人に馴染みの深い檜の香りには、リフレッシュ効果はもちろん、防虫、抗菌、消臭効果もあるといわれています。杉工場の引き出しはすべて無塗装仕上げ。自然本来の色や香りをお楽しみください。
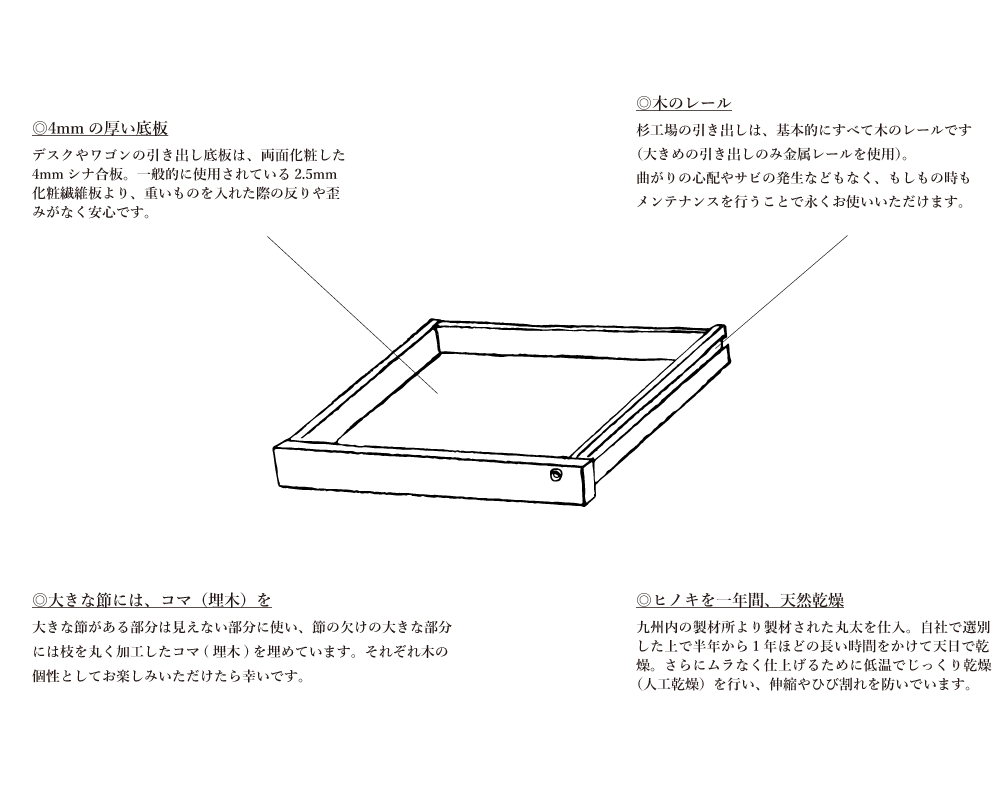
手間と時間をかけてこそ
引き出しを作るために仕入れたヒノキ材は、入荷後すぐに製品化されるわけではありません。自社工場内で選別を行い天日に干すこと、半年から1年。それから更にいくつもの製造工程を経て、一つの引き出しが完成するのです。
非効率的で時間も手間もかかりますが、これらの作業を自社工場内で一貫して行うからこそ、木材を無駄なく使うことができ、檜本来の特性を活かすことができると考えています。
1.職人の目による、木の選別作業
引き出しを作るために、まず製材されたヒノキ材の丸太を一本分まるごと仕入れ、杉工場内で選別を行います。選別作業は1本1本、目で見て手作業で仕分けをします。真夏も真冬も屋外で行う地味で根気のいる作業ですが、木を活かすためのとても重要な作業になります。
板の両面綺麗なものはAランク、節の個数や程度によってBランク、Cランク…など、独自の基準で仕分けを行います。節が目立つものはなるべく見えにくい箇所に使うなど、材の個性にあわせて適材適所で使います。こうすることで、本来は捨てられてしまうかもしれない木材を活用することができます。
2.板材の山を、また一から積みなおす。
木は切られてもなお生きています。水分を多く含んだ状態で届いた原料でそのまま製造してしまうと、乾燥が進むにつれ伸縮や変形が発生し、家具になった後に大きな伸縮や変形の原因となってしまうのです。そのため、板と板の間に桟木(さんぎ)を挟み乾燥を促します。選別作業で仕分けた板材の山を、また一から積み直すのです。
3.半年から一年間、天日に干す
桟木は乾燥させる木材の厚みによって使い分けながら、精確に積み上げていきます。こうして約半年~1年ほど天乾(てんかん/天然乾燥)します。風が吹き、雨が降り、雪がつもる、自然に近い状態でゆっくり時間をかけて乾燥させることで、木の細胞を壊すことなく、木本来が持つ色艶や強さ、香りを引き出すことができると考えています。
4.窯のような乾燥室でさらに乾かす。
さらに天乾だけでは乾燥状態にムラが出るため、人乾(じんかん/人工乾燥)も行います。木材の水分量が均一になり、製品になった際の反りや狂いがより緩和されるためです。といっても高温で一気に乾燥さるわけではありません。乾燥室という大きな窯のような建物に材料を入れ、水分を与えては低音で温める…という作業を繰り返します。非効率な手法かもしれませんが、じっくりと時間をかけて乾燥させることで、木材への負荷を最小限に抑え、木本来の香りや特性を活かせるのではないかと私たちは考えます。
5.上質なヒノキ材を使い、組み立てる。
最後に、ヒノキ材をカットし引き出しとして組み立てていきます。重みに耐えられるよう底板には4mm厚のシナ合板を使用。節の部分はなるべく見えにくい部分に使い、節の欠けの大きな部分には枝を丸く加工したコマ(埋木)を埋めるなど、廃材を出さないよう創意工夫しています。また、曲がるリスクやサビの発生などを考慮して金属のレールは使わず、木のレールで構成しています(大きめの引き出しのみ金属レールを使用)。職人たちの手により組み立てられ、検品を経て、ようやく、ひとつの引き出しが完成します。
ここまでするのは、こどもの頃から使う家具だから
平成初期、海外の協力工場で桐材の引き出しを作っていました。当時、社長が技術指導のため現地を訪れ、桐材を漂白する現場を見学。息をするのもためらうほどの強烈な匂いが鼻を突いたと言います。その時「こんな材料でつくったものを子どもたちに使わせるわけにはいかない」と猛省し、直ちに国内生産に切り替え、現在のスタイルに至りました。九州産ヒノキの中には間伐材も一部含まれています。杉工場が使用するのは微々たる量かもしれませんが、適切に管理された良い材を無駄なく使うことで、また、永く使ってもらえる家具を目指すことで、山や森の維持に少しでも貢献できればと思います。